Definition of Manufacturing Execution System (MES)
A Manufacturing Execution System (MES) is a software system designed to monitor and control production processes on the factory floor or manufacturing facility.
PRODUCTMANUFACTURING EXECUTION SYSTEM
Farid
8/7/202410 min read
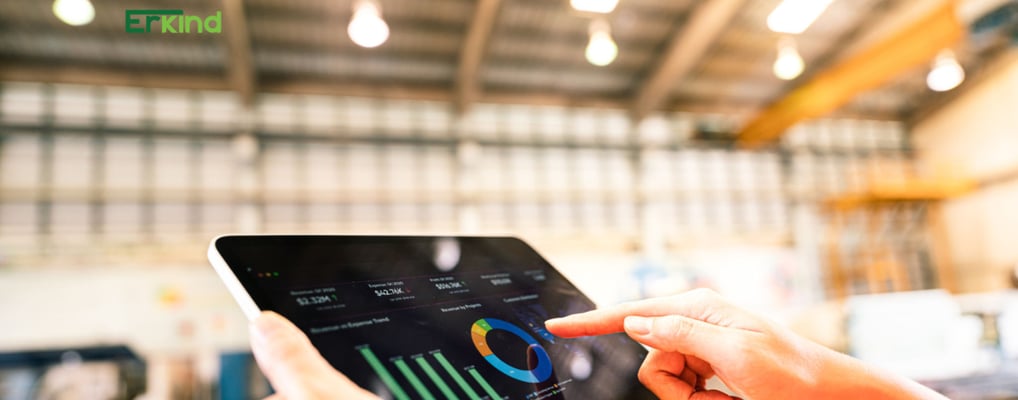
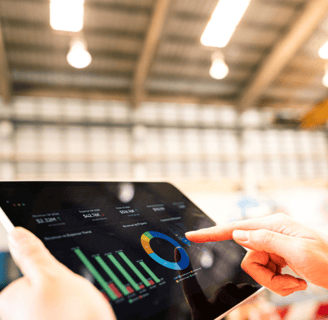
MANUFACTURING
EXECUTION
SYSTEM
A Manufacturing Execution System (MES) is a software system designed to monitor and control production processes on the factory floor or manufacturing facility. The main goal of MES is to optimize the production process, improve efficiency, and ensure product quality by linking higher planning systems (such as ERP) with actual production equipment and processes.
Definition of MES
Manufacturing Execution System definition is a system that manages, monitors, and controls production processes from the plant floor level to the managerial level. MES Manufacturing Execution System Definition acts as a link between the enterprise planning system and the production automation control system. The MES serves to provide accurate and real-time information regarding production status, machine performance, and product quality, thus enabling better decision-making and responsiveness to changing production conditions.
Table of Content :
The Role of Manufacturing Execution System (MES)
The role of the Manufacturing Execution System (MES) in manufacturing is crucial as it bridges the gap between strategic planning and daily operations on the production floor. MES has several important roles that affect almost every aspect of the manufacturing process. Here are some of the key roles of MES in manufacturing:
1. Improved Operational Efficiency
Production Schedule Management: MES assists in real-time production planning and scheduling, optimizing machine and manpower usage to minimize downtime and maximize throughput.
Process Control: By directly monitoring the production process, MES can set and optimize machine parameters to increase efficiency and reduce waste.
2. Product Quality Improvement
Quality Control: MES enables monitoring of product quality throughout the production process, including real-time testing and inspection. This data helps in detecting and addressing quality issues early.
Tracking and Traceability: With the ability to track raw materials, components, and finished products, MES enables identification of the source of quality issues and prompt corrective action.
3. Data Collection and Analysis
Real-Time Data: MES collects data from various sources on the plant floor, including machines, sensors, and operators. This data provides deep insight into production performance and aids in decision-making.
Reporting: MES generates detailed reports on production performance, machine efficiency, and product quality, which can be used for strategic analysis and planning.
4. Resource Management
Raw Material Management: MES manages the allocation and use of raw materials, monitors inventory and ensures that the necessary materials are available when needed.
Labor Management: MES assists in the scheduling and allocation of labor, ensuring that operators and technicians are available and working efficiently.
5. Responsive to Change
Rapid Adaptation: MES enables plants to respond quickly and effectively to changes in market demand, production disruptions, or product design changes.
Change Management: MES can manage changes in the production process and ensure that they are implemented consistently throughout the plant.
6. System Integration
Connection with ERP and SCADA: manufacturing execution system software integrates data from Enterprise Resource Planning (ERP) and Supervisory Control and Data Acquisition (SCADA) systems, ensuring consistent and accurate information across the organization.
Process Coordination: MES serves as a link between top-level planning systems and automation control systems, bridging the gap between strategy and execution.
7. Compliance and Documentation
Regulatory Compliance: MES assists in meeting industry regulatory standards by ensuring that production processes are well documented and comply with quality and safety requirements.
Audit and Documentation: The system keeps detailed records of all production activities, which can be used for auditing and compliance.
8. Improved Visibility and Control
Process Visualization: MES provides a visual display of the production process, allowing operators and managers to better monitor and control operations.
Performance Control: With real-time information on machine and process performance, MES enables better control and faster decision-making.
Overall, MES acts as a vital tool in improving efficiency, quality, and responsiveness in manufacturing, and supports better integration and coordination between various aspects of the production process
MES Overview
1. Main Functions of MES:
Production Process Monitoring and Control: Collects real-time data from production equipment and ensures that the process is running according to plan.
Production Management: Manages production schedules, resource allocation, and production planning to improve efficiency.
Quality Management: Monitoring product quality throughout the production process and recording related data for quality analysis.
Data Collection and Reporting: Collect production data, analyze machine performance, and generate reports that aid in planning and decision-making.
Tracking and Traceability: Tracks raw materials, components, and finished products from the beginning to the end of the production process to ensure transparency and compliance.
2. MES Components:
User Interface: Used by operators and managers to monitor and manage the production process.
Database: Stores production data, machine information, and quality data.
Control Module: Organizes and manages specific functions such as production schedules, machine control, and raw material management.
Integration: Connects with other systems such as ERP (Enterprise Resource Planning), SCADA (Supervisory Control and Data Acquisition), and other process control systems.
3. MES Benefits:
Production Efficiency: Reduces machine downtime, speeds up production cycle time, and optimizes resource usage.
Product Quality: Improves product consistency and quality through better monitoring and control.
Responsiveness: Enables quick reaction to changes in market demand, production disruptions, or quality issues.
Visibility and Reporting: Provides data and reports that aid in performance analysis and strategic planning.
4. MES Implementation Challenges:
Cost and Complexity: MES implementation can be costly and complex, requiring deep integration with existing systems and processes.
Training Needs: System users need to be trained to understand and utilize MES functionality effectively.
Process Changes: Adaptation to new or updated production processes may require major changes in procedures and work habits.
Overall, MES plays an important role in the digital transformation of factories by providing in-depth visibility and better control of the production process, thus helping companies improve efficiency, quality, and competitiveness.
Core Functions of MES
1. Production Planning and Scheduling
Production Planning: MES assists in planning production activities by identifying and structuring the requirements of raw materials, labor, and equipment to meet product demand. This planning includes the creation of short-term and long-term plans that match production capacity and market demand.
Production Scheduling: MES draws up a detailed production schedule taking into account order priority, machine capacity, and raw material availability. This scheduling ensures that orders are processed according to an efficient sequence and set turnaround time. Good scheduling minimizes lead times and maximizes resource usage.
Resource Optimization: MES optimizes the allocation of resources such as machines, manpower, and raw materials, based on the production plan. This helps in avoiding bottlenecks and reducing downtime, as well as ensuring that all resources are utilized effectively.
2. Shop Floor Control
Production Process Monitoring: MES provides direct visibility into the production floor by monitoring all ongoing activities. This includes machine status, production speed, and material usage. With tight control, MES ensures that the production process runs according to plan and quality standards.
Process Control: This system enables real-time setting and control of production parameters. For example, the MES can set the machine speed, reset the machine, or modify the process based on the data collected. This ensures that the production process follows established procedures.
Problem Solving: With real-time data, MES helps in detecting and addressing issues that may arise on the production floor, such as machine breakdowns or quality degradation. The system enables quick response and reduces unplanned downtime.
3. Quality Management
Implementation of Quality Control: MES facilitates the implementation of quality control procedures by setting quality standards and monitoring their compliance throughout the production process. The system can organize quality checks at critical points in the production process to ensure the final product meets the desired specifications.
Nonconformance Management: When a non-conformance or quality issue is discovered, the MES records the incident and assists in the corrective action management process. The system documents deviations, cause analysis, and corrective measures to prevent similar issues in the future.
Audit and Compliance: MES supports quality audits by providing complete data on each step of the production process, including the results of quality checks and corrective actions taken. This facilitates compliance with industry standards and regulations.
4. Data Collection and Analysis
Production Data Collection: The MES collects data from various sources on the production floor, including machines, sensors, and operators. This data includes information on production speed, raw material consumption, downtime, and quality parameters.
Data Analysis: The MES analyzes the collected data to provide insights into production performance, process efficiency, and product quality. This analysis helps in identifying trends, patterns, and areas that require improvement.
Reports and KPIs: MES generates regular reports and key performance indicators (KPIs) that measure various aspects of production performance, such as machine efficiency, defect rates, and resource utilization. These reports and KPIs provide a clear picture of how operations are running and which areas need improvement.
Overall, the core functions of MES are designed to improve efficiency, quality, and control in the production process. With proper planning and scheduling, tight control on the production floor, good quality management, and effective data collection and analysis, MES helps companies better achieve their production goals and ensure that the products produced meet the expected standards.
Benefits of Manufacturing Execution System Implementation
The implementation of MES (Manufacturing Execution System) provides a number of significant benefits to manufacturing companies. With MES, companies can improve production efficiency through automation of routine tasks and real-time performance monitoring. Product quality also improves thanks to better quality control and faster identification of problems. In addition, MES helps optimize inventory management, reduce production costs, and provide better visibility over the entire production process. Thus, MES becomes an invaluable tool for improving the productivity, flexibility, and competitiveness of companies.
1. Efficiency and Productivity Improvement
Production cycle time optimization: MES helps identify and eliminate bottlenecks in the production process, so that production cycle time can be shortened significantly.
Reduction in machine setup time: With better production planning, the time required to prepare machines for the next production can be minimized.
Improved OEE (Overall Equipment Effectiveness): MES enables real-time monitoring of machine performance, so that machine downtime can be minimized.\
2. Product Quality Improvement
Real-time quality monitoring: MES enables monitoring of product quality at every stage of production, so that quality issues can be identified and addressed quickly.
Improved compliance with standards: MES helps ensure that the products produced meet all applicable quality standards and regulations.
Reduction of product defects: With faster identification of quality issues, the number of defective products can be significantly reduced.
3. Better Inventory Management
Accurate material requirement planning: Manufacturing Execution Systems (mes) helps in more accurate planning of material requirements, so that companies can avoid excess or shortage of inventory.
Reduced storage costs: With better inventory management, companies can reduce storage costs.
Increased material availability: MES ensures that the required materials are always available at the right time.
4. Increased Visibility and Control
Full visibility over the production process: Manufacturing Execution System provides a comprehensive overview of the entire production process, from planning to delivery.
Improved collaboration between departments: MES facilitates collaboration between the various departments involved in the production process.
Better decision-making: With accurate and real-time data, management can make better and faster decisions.
5. Cost Reduction
Reduction of production costs: By improving efficiency and productivity, MES can help reduce production costs significantly.
Labor cost reduction: Automation of routine tasks can reduce the need for labor.
Reduction in storage costs: Better inventory management can reduce storage costs.
MES Implementation and Integration
The implementation and integration of a Manufacturing Execution System (MES) is an important step in improving the efficiency and quality of production processes in manufacturing companies. Here are the key factors for a successful MES implementation, challenges that may be faced, as well as best practices to overcome these challenges:
Key Factors for Successful MES Implementation
1. Careful Planning
Needs Assessment: Conduct a thorough analysis to understand the specific needs of the company. Identify the processes to be automated and improved, and how the MES will support business objectives.
Clear Objectives: Set clear and specific goals for MES implementation, such as increased efficiency, reduced downtime, or improved product quality.
2. Stakeholder Engagement
Team Involvement: Involve all stakeholders from the beginning, including IT teams, production, and plant managers. Their involvement is important to understand their needs and gain support for implementation.
Training and Education: Ensure that end users are adequately trained on how to use the MES and the benefits they will gain.
3. System Design and Customization
Customized System Design: Tailor the MES design to the production process and specific needs of the company. Ensure that the system can integrate with existing systems, such as ERP (Enterprise Resource Planning) and automated control systems.
Effective Customization: Make customizations where necessary, but avoid excessive changes that can complicate the system. Focus on features that add immediate value.
4. Integration with Other Systems
Seamless Integration: Ensure that the MES is integrated with other existing systems in the company, such as ERP, SCM (Supply Chain Management), and automated control systems. Good integration ensures a smooth flow of information between these systems.
Data Consistency: Maintain data consistency across systems. Accurate and consistent data is essential for informed decision-making.
5. Change Management
Change Management Strategy: Implement a change management strategy to help employees adapt to the new system. Communicate the benefits of MES effectively and provide support to overcome resistance to change.
Phased Approach: Consider implementing MES in phases, starting with specific areas or processes, before expanding to the entire organization. This allows for testing and customization before full implementation.
Challenges and Best Practices
1.Challenges: Cost and Budget
Best Practice: Create a realistic budget and plan for additional costs that may arise during implementation. Consider the cost of licenses, hardware, training, and technical support in the budget.
2. Challenge: System Integration
Best Practice: Choose an MES solution that is designed for easy integration with existing systems. Use open standards and protocols to facilitate integration. Work with system providers and consultants who have experience in system integration.
3. Challenge: User Resistance
Best Practice: Involve end users in the implementation process from the beginning. Provide comprehensive training and ongoing support. Clearly communicate the benefits of MES to reduce resistance.
4. Challenges: Data Complexity
Best Practice: Ensure the MES system has the ability to effectively manage and analyze data. Use powerful analytics tools to process and present data in a way that is easy to understand and actionable.
5. Challenge: System Security
Best Practice: Implement stringent security measures to protect production data and MES systems from cyber threats. This includes the use of encryption, access control, and periodic security audits.
6. Challenge: Technical Support and Maintenance
Best Practice: Choose an MES provider that offers good technical support and maintenance services. Consider creating a maintenance and support plan to ensure that the system remains in good working order after implementation.
7. Challenge: Scalability and Flexibility
Best Practice: Choose an MES system that can be easily scaled and adapted to changing needs. A flexible system will be more adaptable to changes in production processes or capacity additions.
Conclusion
Manufacturing Execution System implementation requires careful planning and support from all parties in the company. However, the benefits derived from this investment are enormous. MES can help companies reduce production cycle time, improve resource utilization efficiency, and increase customer satisfaction. Interested in implementing MES in your company? Contact us for a free consultation and find the right solution for your business.
Location
Indonesia Stock Exhange Tower 1 Level 3 Unit 304 Jl Jendral Sudirman KAV 52-53, Senayan, Kebayoran Baru, Kota Adm Jakarta Selatan DKI, 12190
Follow Our Social Media
Contacts
021-5890 5002
admin@erkind.com
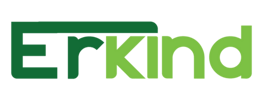
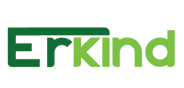